Closing the loop: innovation within hard-to-abate construction materials
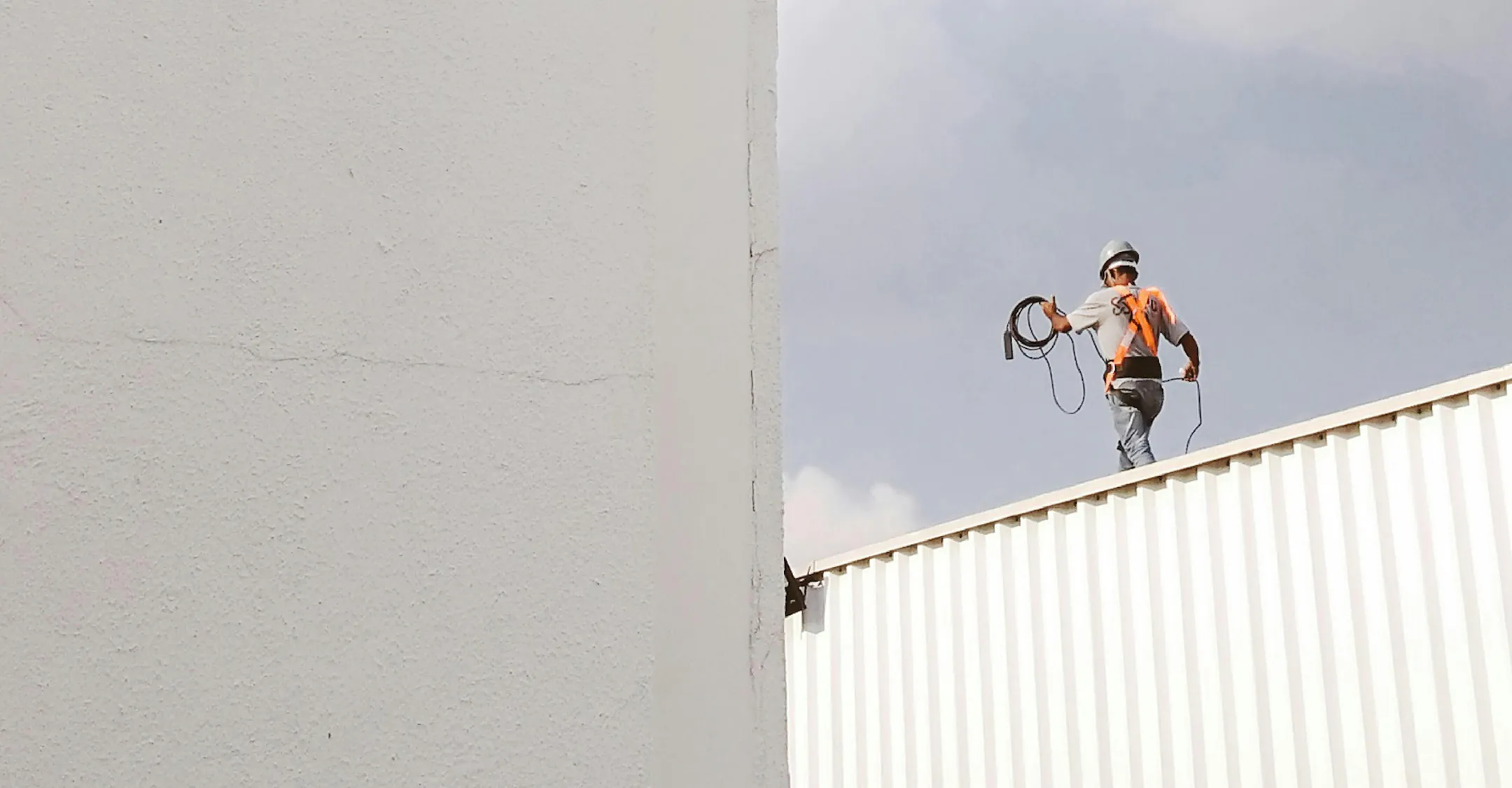
To address the expanding global population, investment in building development and infrastructure is necessary. Housing shortages persist in many societies, with an estimated 75% of buildings needed by 2050 yet to be constructed. Meeting this demand requires about 30 billion square meters of new construction, equivalent to the size of New York City, every 40 days.
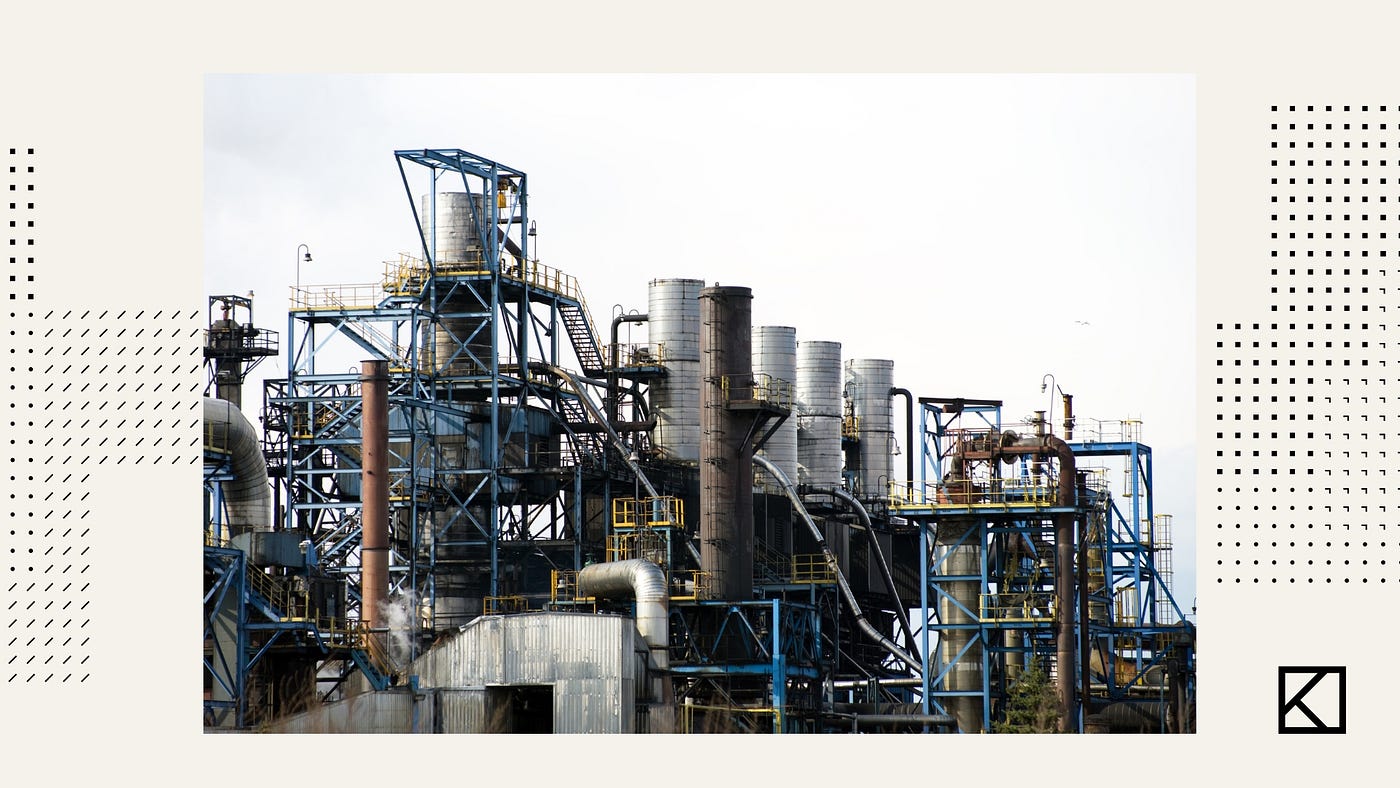
However, this rapid growth carries a significant environmental toll if traditional materials and construction methods persist. Currently, the built environment contributes to 37% of global CO2 emissions, 40% of energy consumption, and 40% of waste, with only about one-third of the 2.2 billion tons of annual construction waste being recycled. The underlying issue lies not in lacking viable technologies and approaches, but rather in incomplete policies and insufficient coordination among stakeholders in the built environment. The construction industry is facing various challenges due to this growing demand for raw materials, affecting building costs, interest expenses, labor availability, and resource availability for both established and emerging companies.
Globally, the construction sector is responsible for approximately 1/3 of total material consumption, contributing to a threefold increase in global material extraction since 1970. New construction activity will continuously increase the demand for natural resources like sand, bauxite, iron, limestone, copper, and gypsum unless we change the way we manage the lifecycle of construction materials. Given that mining contributes significantly to habitat destruction, soil erosion, and groundwater contamination, the rate at which we reuse existing construction materials will be critical to improving the building industry’s environmental footprint.
Adopting the circular economy model offers opportunities to reduce raw material extraction, develop sustainable alternatives, utilize waste, and prolong product life. However, scaling the supply of reclaimed materials and ensuring their safety and compliance with local building codes is a major barrier to overcome.
Circularity isn’t just about being eco-friendly; it’s also about helping construction companies secure their supplies and spend less on new materials.
Martin Pauli, Director and Global Leader Circular Economy Services, from global sustainable development consultants ARUP, explains how many companies operate on slim margins and could lose their licenses if raw material prices keep rising: “To deal with these challenges, companies need to rethink how they get materials, focusing on reuse and renewable options to lessen the impact of rising prices. The move toward circularity doesn’t always mean lower costs; it currently relies heavily on labor-intensive methods, underscoring the need for technological advancements to boost productivity. Countries like the Netherlands, Scandinavia, and France, which have adopted whole-life carbon targets for buildings, show notable progress in circularity, emphasizing the importance of reusing, reclaiming, and recycling materials to meet decarbonization goals. As we look ahead, a comprehensive examination of the materials value chain, starting from raw material mining, suggests a shift in dynamics over the next 10–20 years, with downstream companies increasingly turning to urban mining and secondary materials, particularly in regions with stringent regulations and policies.”
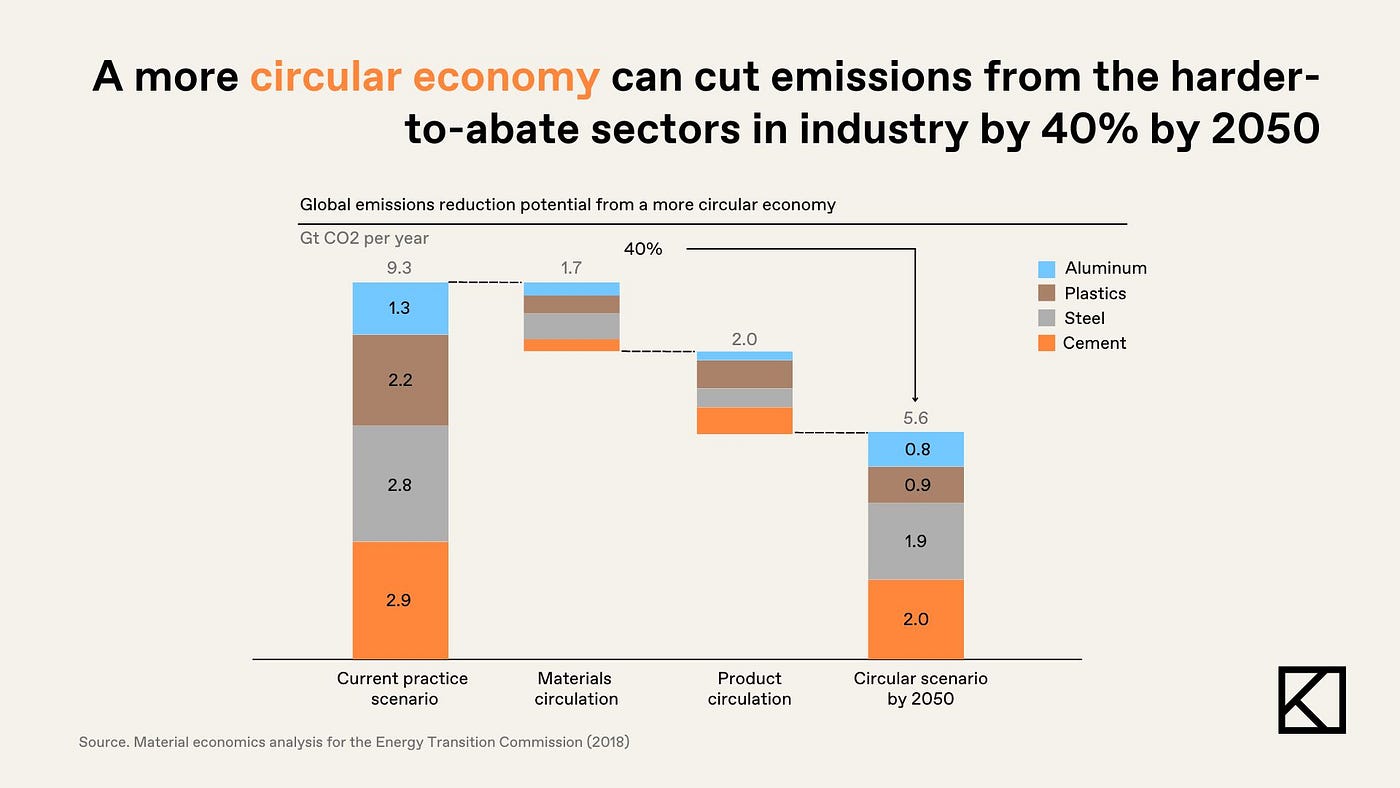
Several industries including cement and concrete, steel, glass, aluminum, and many more are at the cusp of technological shifts that can dramatically improve their environmental track record. In this article, we will focus on cement and concrete, steel, and aluminum, acknowledging that other hard-to-abate materials like glass are also undergoing technological transformation.
Cement and concrete
When considering the future role of cement alongside emerging low-carbon materials like wood, it is evident that cement and concrete will remain essential in construction, albeit with efforts to reduce carbon emissions. Martin explains: “Essential components such as foundations and building structures will continue to rely on concrete. However, there will be a gradual exploration of alternatives”. Global concrete production volume surpasses that of all other materials combined, constituting 8% of greenhouse gas emissions. Despite its durability and recyclability, concrete recycling remains a niche practice due to incomplete regulatory frameworks, market drivers, and limited awareness. “Innovation is more widespread in regulated environments, while less regulated countries often adhere to linear production models”, Martin adds.
One of the most promising methods of enhancing concrete’s circularity is by using waste streams from other industries in its initial production. In place of newly mined limestone and clay needed to produce clinker, the main constituent in cement, mine tailings and other byproducts such as coal fly ash or blast furnace slag can be utilized. Waste streams also have the potential to be used as alternative fuel sources to power cement kilns, replacing coal and significantly reducing the sector’s emissions profile. The recovery of waste streams is projected to add $116 billion value to the concrete industry by 2050 while eliminating 1.5 billion tons of CO2. Material Evolution, a KOMPAS portfolio company, is making meaningful contributions to this shift by using a geopolymer that incorporates waste streams from the steel industry in a process that requires no heat. The result is a cement with a CO2 footprint 85% lower than traditional products.
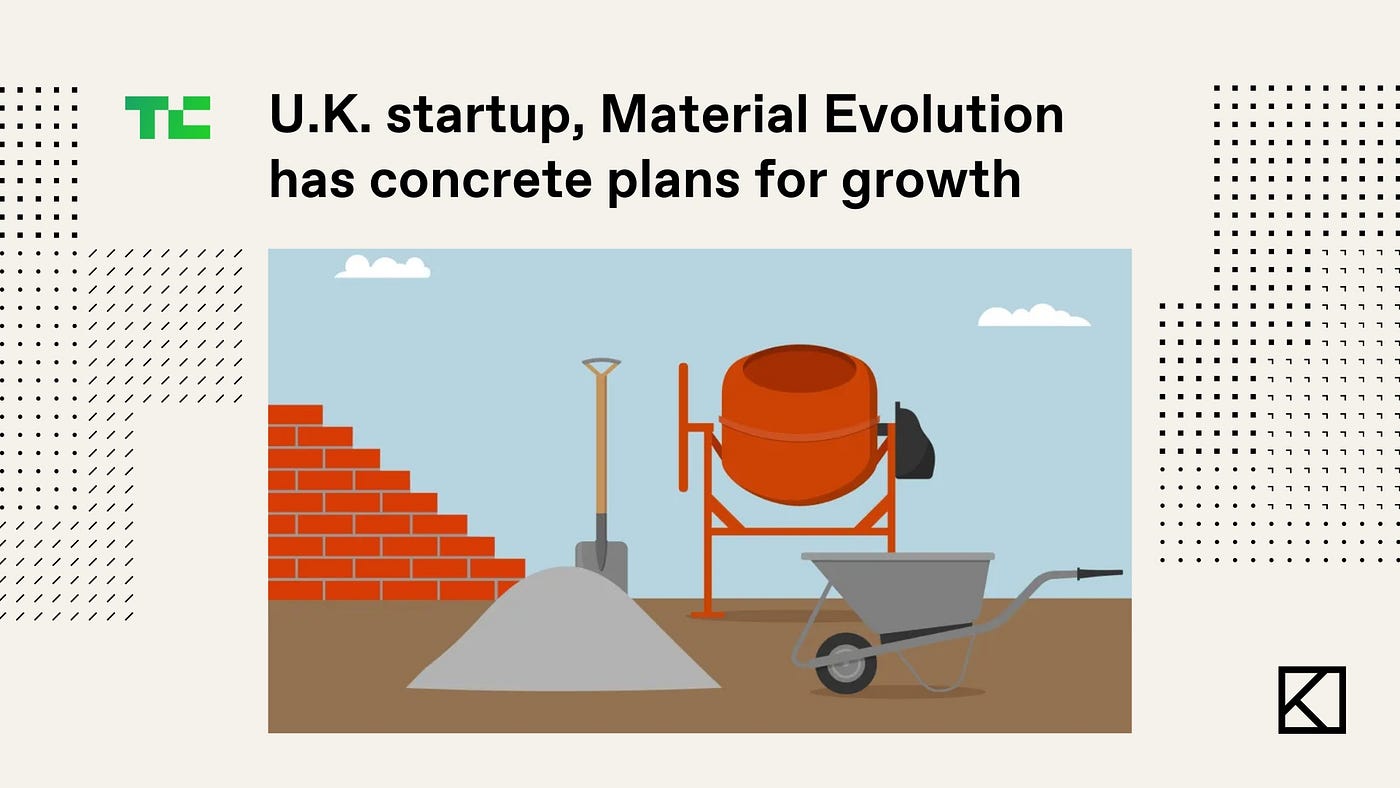
Steel
Every year, an estimated 2.2 billion tons of steel are produced globally, with half allocated to construction, contributing a further 7% of global emissions. Transitioning to a circular steel sector involves improving material and process efficiency, increasing steel recycling rates, and integrating renewable energy sources in its’ production. While recycling rates have reached approximately 85%, significant efforts are still needed to achieve a fully circular lifecycle for steel. Enhancing material efficiency includes advancements in alloy strength to prolong structure lifespans, reducing replacements, and minimizing resource consumption by constructing stronger, lighter buildings. Additionally,the shift from traditional blast furnaces to electric arc furnaces, hydrogen-powered production, or innovative thermal-based furnaces like those designed by HELIOS, a KOMPAS portfolio company, is crucial for reducing the industry’s carbon footprint.
Furthermore, there’s a growing emphasis on steel recycling, where specialized companies extract steel from various sources, assess its integrity, and distribute it to secondary markets. Although this shift holds promise for reducing the carbon footprint associated with steel production, challenges persist, particularly regarding regulatory frameworks for recycled steel.
Aluminum
Aluminum is the most widely available metal in the world, making up roughly 8% of the world’s crust. It is a highly desired material due to its light weight, flexibility, and oxidation resistance. Aluminum is a critical metal for the clean energy transition as it is needed for the construction of solar, EVs, windmills, and heat pumps. The aluminum sector is already somewhat circular, with approximately 75% of all aluminum ever produced still in use today. However, addressing the remaining 25% of low-grade aluminum scrap requires technological innovation, explains Martin Pauli from ARUP: “Advanced companies are using artificial intelligence (AI) to efficiently filter materials and separate low-grade fractions. By fine-tuning industrial processes with innovative technologies, there’s significant potential to overcome technological barriers and increase the efficiency of aluminum recycling.”
While aluminum is theoretically infinitely recyclable, challenges like alloy contamination and limitations in sorting technologies hinder recycling optimization. To achieve circularity in the aluminum value chain, increasing recycling rates through improved sorting technologies, reducing process emissions by transitioning from carbon to inert anodes during smelting, and using renewable fuels for energy-intensive production processes like calcination and smelting are key opportunities. Like cement and steel production, integrating waste streams into aluminum production processes can enhance efficiency and reduce emissions. For instance, extracting clean stored energy, such as hydrogen and steam, from second-life aluminum scrap, and recovering critical alumina inputs from post-consumer scrap can significantly diminish the need for additional bauxite ore mining. By incorporating additional circular loops, it’s estimated that emissions from aluminum production could plummet by 89% by 2050, while also adding an anticipated $42 billion in value to the aluminum industry.
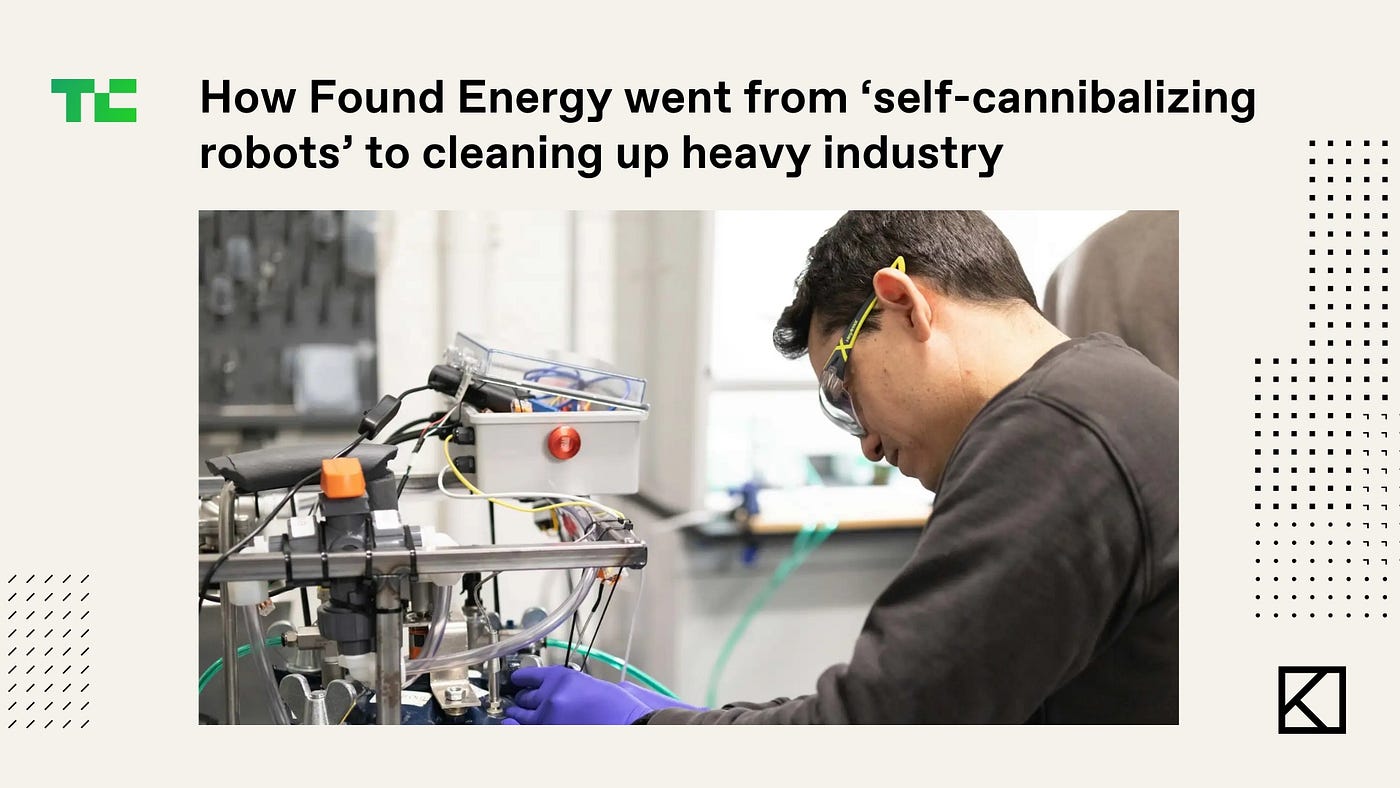
Discussion
As identified by the Circular Buildings Coalition, adopting circular economy principles in the built environment would bring significant environmental, economic, and societal benefits. This optimization relies on significantly increased collaboration between industry stakeholders across the value chain. Innovation around capturing the value and opportunity of more circular approaches through a project’s lifecycle, digital tools to improve transparency, knowledge and information sharing, and innovative techniques to incorporate circularity into mainstream materials are all critical to gaining traction.
Circularity is important in materials production and integrating it into all stages of the building process is essential. Whole buildings can be designed to be circular, effectively serving as materials banks. This holistic approach ensures that resources are utilized efficiently, and that waste is minimized, contributing to a more sustainable built environment.
The policy landscape is evolving to increase responsibility for carbon impacts, however more comprehensive policies and regulatory frameworks are required to bring circular solutions to scale. Encouragingly, initiatives like the EU Green Deal have spurred substantial investments in the market, including from private equity. Circular solutions are increasingly viewed as future-proof investments. Clear and deliberate legislation can create signals to industrial players for investment in technologies and solutions that support the realization of a circular built world. Some potentially significant drivers of change to incentivize companies to promote circularity include stricter carbon tax frameworks and landfill usage penalties. Future-forward industry players will anticipate the needs of a changing world and strive to adapt from a linear material landscape to a circular one. Those who make changes to their business models and processes early and increase their levels of collaboration stand to benefit the most and capture the most value in a circular economy.
It’s important to acknowledge that transformations and innovations typically require significant capital expenditure (CAPEX), necessitating investment from both private and public sectors. Furthermore, risk remains a significant challenge, particularly within the conservative construction sector, highlighting the importance of engaging in pilot projects to confirm feasibility, establish credibility, and foster trust among stakeholders. These projects can help steer the industry towards embracing new solutions. However, it’s vital not to draw overly broad conclusions from pilot initiatives. Instead, a thoughtful approach is needed, considering factors like economies of scale and long-term cost dynamics — contributory factors to the industry’s fragmentation. In construction, this fragmentation frequently impedes the ability to capitalize on optimal outcomes, with focus directed towards individual projects rather than overarching industry trends.
Achieving circularity requires collaborative efforts across value chains. When companies collaborate — such as product manufacturers partnering with logistics or demolition firms — it unlocks opportunity and promotes mature business models and market consolidation. This consolidation is vital for promoting sustainable growth.
Conclusion
While circularity serves as our guiding principle, it’s clear that not everyone in the industry has fully adopted this concept and approach. We at KOMPAS are confident that the normalization of circularity in the built world is a matter of when, not if, and are eager to back the innovative builders in this space.
— by Summit Rosenberg, Investment Associate at KOMPAS VC